One major factor in achieving high-quality screen prints is the mesh count of the mesh on your screen printing frames. Understanding mesh count and its significance will impact the outcome of your prints. Mesh count plays a pivotal role in the screen printing process, directly influencing the quality, detail, and ink deposit of the final print. Understanding the characteristics of different mesh counts empowers printers to make informed decisions, resulting in superior prints that accurately reflect the intended design.
What is Mesh Count and How is it Measured
Before going in depth of the different mesh counts and when to use them, let's start with a baseline definition of what is mesh count. When screen printers talk about mesh count, they are referring to a measurement of how many threads of polyester (which used to be silk, centuries ago, hence ‘silkscreening’) cross each other per square inch of the screen. For example, a 110 mesh screen would have 110 threads crossing per square inch.
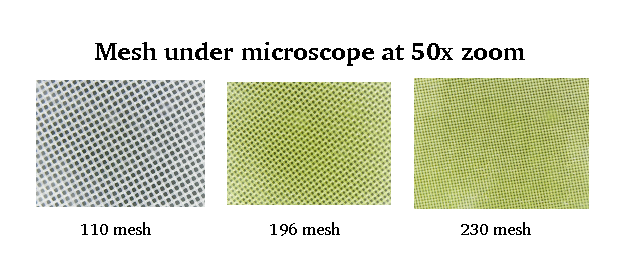
Screen printing meshes vary in count, typically ranging from 36 to 408 threads per inch. Each count serves a specific purpose, offering distinct advantages based on the type of design, ink, and material being printed. Two of the most common mesh count frames are 110 and 156.
A mesh count of 110 will lay down a fairly thick layer of ink. This mesh is great for block text letters and larger spot color designs. It’s also a very common mesh for your underbase when manual printing because you will only have to do one pass, which speeds up your production times.
A mesh count of 156 is also fairly standard and will lay down a moderate amount of ink, but offers more detail for your image.
When switching from manual printing to automatic printing, most screen printers should raise their mesh counts. Many manual printers like the lower mesh counts because it is easier to print with because it takes less effort to push ink through a lower mesh count. However, with an automatic printing machine, that is factored out since you are no longer pushing (or pulling) the squeegee. For example, if you were using a 110 mesh for an underbase, switch to a 125 mesh when printing on an automatic screen printing machine. It will provide the same underbase coverage while allowing a lighter, softer feel to the finished print.
Selecting the Right Mesh Count
The choice of mesh count is like selecting the perfect brush for a painter or the ideal lens for a photographer. Each mesh count has its own set of advantages and disadvantages. Whether it's the desire to create bold, vibrant designs on heavy textiles or intricate, detailed artwork on delicate surfaces, understanding the nuances of low, medium, and high mesh counts is key to a successful print.
These variations in mesh counts allow for different ink deposition, detail precision, and substrate adaptability. To simplify things for this article, we will break down mesh counts into three different categories: lower count, medium count, and high count screen mesh.
- Lower Mesh Counts (15-100): Screens with lower mesh counts have larger openings between the threads, allowing thicker inks to pass through easily. They are suitable for printing on heavier substrates like sweatshirts, tote bags, and other textiles where a heavier deposit of ink is desired. Additionally, these lower counts are ideal for printing opaque designs on dark fabrics, as they allow more ink to pass through, ensuring better coverage. The most common use of lower count mesh is for glitter and shimmer inks. These inks are made special to have flakes of glitter in them to give the desired look - which won’t be able to pass through higher count mesh. A mesh size of 36 is fairly common for glitter inks, although you can go up to a 64 mesh on these inks. For shimmer inks, an 86 mesh is recommended.
- Medium Mesh Counts (110-180): These counts strike a balance between ink deposit and fine detail. They are versatile and work well with various types of ink and substrates, making them a popular choice for general-purpose printing. Medium mesh counts are suitable for printing on T-shirts, posters, and other common materials.
- Higher Mesh Counts (200+): Screens with higher mesh counts have finer openings, enabling the printing of intricate details and achieving a smoother finish. They are ideal for designs with fine lines, halftones, and detailed artwork. These high mesh count frames work exceptionally well with thinner inks and are perfect for printing on smoother surfaces like paper and thinner fabrics. The higher mesh count also helps to keep the thinner inks from flooding onto your substrate. If you want a softer hand feel to your plastisol prints, these higher mesh counts can help with that as well. While plastisol prints may feel softer with higher mesh counts, you will probably sacrifice the opacity of the ink when using a higher mesh count. If your design is meant to have very bright, vibrant colors, pay attention to how much ink is getting through to your material.
The Importance of Choosing the Right Mesh Count
Selecting the appropriate mesh count is critical for achieving the right print quality. Using a mesh count that is too low for a detailed design can result in ink bleeding and a lack of definition, while using a high mesh count for a design requiring heavy ink coverage might lead to insufficient ink passing through.
Considering type of artwork, thickness of ink, amount of ink to deposit, the substrate material, and the level of detail are all factors you want to consider when choosing the mesh count. Experimentation and testing on sample materials is the best way you can determine the right mesh count for your particular project.
Whether you're aiming for bold, opaque prints or intricate, detailed designs, the right mesh count ensures that your screen printing projects achieve the desired outcome. By considering the nuances of mesh counts, printers can elevate their craft and produce stunning, professional-quality prints.
Why Thin Mesh Threads Are Not Worth the Cost
The choice between thin and standard threads for screens can significantly impact the quality and precision of the final print. These threads refer to the diameter or thickness of the individual strands that compose the mesh. Considering the differences between thin and standard threads is also a factor that printers seeking specific outcomes in their designs take into consideration.
Thin Threads:
Screens with thin threads are characterized by their finer and more delicate strands. These thinner threads allow for higher mesh counts within a given area, facilitating the printing of intricate details and fine lines with exceptional clarity. The smaller openings between threads also enable the use of thinner inks, contributing to sharper image reproduction and smoother gradients.
However, while thin threads excel in capturing fine details, they have limitations in terms of ink deposit capacity. They are not suitable for designs that require a heavier application of ink or when printing on thicker materials due to their relatively smaller thread diameter. Additionally, thin thread mesh rips and tears more easily, along with being more expensive. Unless you are printing highly intricate 10+ color designs, save your money. You do not need thin threads.
Standard Threads:
Conversely, screens with standard threads feature thicker strands, offering greater durability and ink deposit capabilities. These screens can handle thicker inks and are well-suited for well over 95% of the screen print jobs shops do. Standard-thread screens strike a balance between ink deposit and detail precision, making them versatile for various types of designs and substrates.
Conclusion
Whether you seek fine, intricate details or robust ink coverage, the mesh choices define your printing capabilities. For tailored guidance and expert assistance in optimizing these crucial elements for your next project, reach out to a screen printing expert at Lawson Screen & Digital Products. Our knowledgeable sales representatives can offer valuable insights and solutions, ensuring that your screen printing projects achieve the precision and quality you need for your customers. Contact us today because at Lawson: We Make It Simple!